在航天器制造領(lǐng)域,"失之毫厘,謬以千里"的嚴(yán)苛要求使得零件加工精度成為決定任務(wù)成敗的關(guān)鍵因素。隨著太空探索向更深、更遠(yuǎn)領(lǐng)域拓展,傳統(tǒng)加工技術(shù)已難以滿(mǎn)足高密度、高性能零件的制造需求。
超聲波二維振動(dòng)平臺(tái)的引入,正為航天零件加工帶來(lái)革命性突破。
一、突破傳統(tǒng)加工極限
超聲波二維振動(dòng)平臺(tái)通過(guò)高頻振動(dòng)(通常15-40kHz)在切削方向疊加微小的振動(dòng)量,使刀具與工件之間形成周期性微切削。在航天鋁合金零件加工中,該技術(shù)可使表面粗糙度從Ra0.8μm降至Ra0.1μm以下,刀具壽命延長(zhǎng)3倍以上。在鈦合金加工領(lǐng)域,振動(dòng)引起的自銳效應(yīng)有效避免積屑瘤形成,使加工效率提升40%。
振動(dòng)平臺(tái)的創(chuàng)新之處在于其可編程特性。控制系統(tǒng)可通過(guò)CAD/CAM軟件實(shí)時(shí)調(diào)整振動(dòng)頻率和幅度,針對(duì)不同曲面特征實(shí)施動(dòng)態(tài)優(yōu)化。這種智能調(diào)控能力使復(fù)雜結(jié)構(gòu)的深腔、薄壁零件加工成為可能,滿(mǎn)足航天器輕量化設(shè)計(jì)需求。
二、助力高精度加工創(chuàng)新
在微型航天零件加工場(chǎng)景中,振動(dòng)平臺(tái)展現(xiàn)特殊優(yōu)勢(shì)。某衛(wèi)星用微型齒輪加工案例顯示,采用二維振動(dòng)平臺(tái)后,齒面波紋度從2μm降至0.5μm以?xún)?nèi),關(guān)鍵尺寸精度穩(wěn)定在±5μm以?xún)?nèi)。在高精度鏡面加工中,振動(dòng)輔助工藝使面形精度達(dá)到λ/10量級(jí),滿(mǎn)足空間光學(xué)元件的要求。
振動(dòng)技術(shù)對(duì)加工材料的熱敏感性問(wèn)題提供了解決方案。在高溫合金零件加工時(shí),振動(dòng)能量促進(jìn)了切屑快速脫離,有效降低切削溫度30%-50%,避免了熱影響區(qū)的形成。這一特性對(duì)碳纖維復(fù)合材料加工同樣適用,顯著提高了層間結(jié)合強(qiáng)度,降低了分層風(fēng)險(xiǎn)。
三、智能制造系統(tǒng)集成
現(xiàn)代超聲波振動(dòng)平臺(tái)與物聯(lián)網(wǎng)技術(shù)深度融合,實(shí)現(xiàn)加工狀態(tài)實(shí)時(shí)監(jiān)控與自適應(yīng)調(diào)整。通過(guò)傳感器網(wǎng)絡(luò),系統(tǒng)可監(jiān)測(cè)振動(dòng)參數(shù)、切削力、溫度等20余個(gè)指標(biāo),當(dāng)檢測(cè)到異常時(shí)立即優(yōu)化參數(shù)設(shè)置。大數(shù)據(jù)分析功能可根據(jù)歷史數(shù)據(jù)預(yù)測(cè)刀具磨損趨勢(shì),提前預(yù)警維護(hù)需求。
四、超聲波二維振動(dòng)平臺(tái)實(shí)拍圖展示
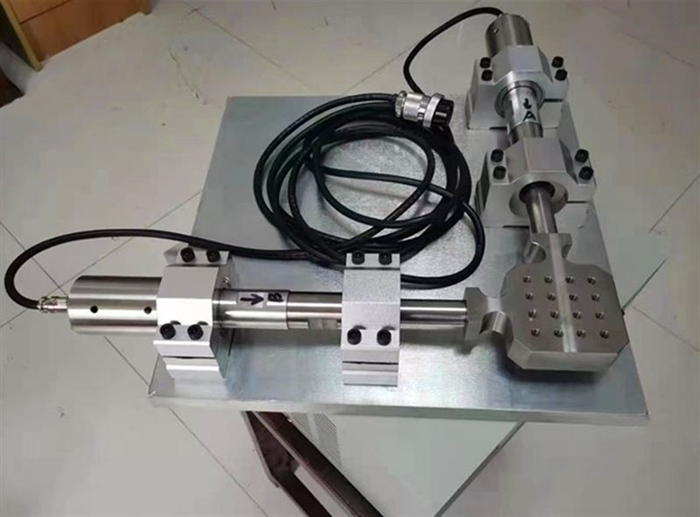
未來(lái),隨著振動(dòng)頻率提升至兆赫茲級(jí)、功率密度增加,其在航天零件微細(xì)加工領(lǐng)域的應(yīng)用將更加廣泛。這種智能加工技術(shù)的突破,不僅提升了制造精度與效率,更為我國(guó)航天裝備的高質(zhì)量發(fā)展提供了堅(jiān)實(shí)的技術(shù)支撐。